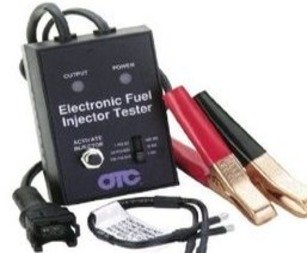
There are times when testing fuel injector’s makes a lot of sense. This page discusses how to do it. You can also get the tools here to accomplish individual test procedures.
EFI testing is often necessary when dealing with a stubborn rough running condition, engine run on after the key is turned off or even poor fuel economy.
I’m sure you’ve seen the commercials about over the counter injector cleaners that fix all kinds of nasty problems. Even more compelling is the advertisements from gas companies.
They say you can drive your engine clean using their premium detergent gasoline. We should take these claims with a grain of salt. Is it possible your car will be healed by this liquid gold? Yes, it’s possible. However, it’s not likely.
Fuel injection services are a popular up sell at many auto repair facilities. Often these cleaners and services are purchased for good measure without knowing if they’re needed.
Nevertheless, these gas delivery components can be pressure drop tested and diagnosed. This means there is no need for guessing. In my opinion you shouldn’t clean an injector unless it’s needed.
Why do I feel this way? On the early GM port fuel type injectors I’ve seen them malfunction after cleaning. Some cleaners are so harsh that they can damage the internal wire winding or harm the spray pattern.
An injector is nothing more than an electrically operated solenoid that’s actuated to allow fuel to flow at a set rate.
Although many think this is a complicated component, the operation is actually quite basic. The solenoid is energized and held open until it delivers the correct amount of gas and then it’s turned off.
Fuel Injector Problems
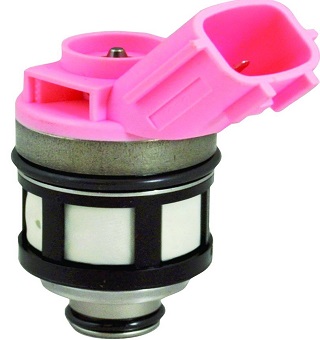
Dirty injectors or ones that have failed completely will either be stuck in the open or closed position.
An injector that doesn’t open can cause hard starts, lack of power and the rough running condition. One that’s stuck partially open can cause a loss of fuel pressure and will allow raw gas to leak into the cylinder.
Eventually the extra liquid work its way down into the oil sump. After this goes on for a while you might be able to pull the engine oil dipstick and notice an over filled oil level condition.
Another sign that fuel is leaking into the oil is the smell of raw gas mixed with the engine oil. The odor is often strong enough that you can smell it on the dip stick when checking the level and condition.
Another telltale sign of a leaking injector is a run on condition.
This is also called dieseling. In other words, the engine can kick and sputter like an old fashioned diesel truck for a few seconds after the key is removed.
When you turn off the key to shut down the engine the injection process stops.The engine should immediately quit. If it continues to run on or clatter and sputter instead of turning off completely and immediately, you have fuel dripping in the combustion chamber.
A dirty injector is a possible cause of the above condition. Build up of gum or carbon deposits on the tip can prevent it from sealing completely when the solenoid is not energized.
This allows raw fuel to continue to enter the cylinder. This is then ignited by heat and compression like a diesel engine. The closer the injector is to the engine the more heat it’s exposed to and the more likely a gummy deposit can develop.
How to Test Fuel Injectors
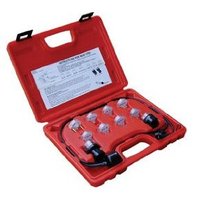
The first thing to do when testing an injector is to make sure the electrical side of the circuit is working correctly.
If you do not get a fire signal no gas will flow to the combustion chamber on that cylinder. The signal itself originates from the power train control module on most types of automobiles.
On some models this is called the injection driver module. However, in both cases it’s a low voltage pulse which makes testing the circuit with a standard test light difficult. Hence time to buy another special tool.
They make a test device that plugs into the injector connector known as a noid light. This will flash when the injector is signaled to open. It stays lit until the unit is closed by the control module.
This can test the entire engine management side on many models. It’s true that you can use an automotive meter for the same test. Although the ease of use by just looking for the flash is nice and hands free.
You can also test the resistance of the injector itself with a multi meter. Resistance should be within a given range. The range specification is dependent on the year, make and model being tested.
The two common things found with a damaged internal wire winding, is high resistance, or an open injector. Open means the delicate internal coil of wire used to create a magnetic field is damaged. A situation requiring replacement parts.
When I find the injectors are firing correctly and electrically sound, the next thing I do is to perform an injector balance test.
This test can help isolate clogged, dirty, or inoperative injectors. Different engines will have different procedures for performing this test and a vehicle specific auto repair manual is recommended for testing.
However, using a GM car as an example, what you do is connect a fuel pressure gauge to the test port on the fuel rail. You turn the key on (engine off) to build pressure in the fuel rail.
This is why the fuel pump runs for at least 2 seconds when the ignition is turned on. You can stop here and watch the gauge to make sure the rail holds this pressure for a few minutes.
Continued leak down could indicate a problem. With the key on and the engine off you then mechanically trigger each one with an electronic fuel injector pulse tester.
The tool I own is pictured at the top of this page or there is a cheaper version I’ve never used available below. After you activate the pulse you then record how much the fuel pressure drops in the rail after each trigger event.
They make injector test equipment in kits to help accomplish these tasks for specific models. This is the way to go if you’re a dealership technician sticking to a single brand of car.
Here’s the important point. When each individual injector is mechanically activated it should drop the fuel pressure in the rail the same amount as on the others.
Manufacturers will usually include a plus or minus tolerance of 2-3 PSI as an allowable variance. If you have one injector that drops 10 PSI and the other injectors drop 25 PSI then the one with the lower flow rate needs to be inspected.
When you’re testing, low pressure drops are the ones to look out for. If the tip or orifice is dirty or restricted you’ll find there won’t be much pressure decrease when it’s energized.
These may need a cleaning with a professional injector cleaning tool. You can get one below. However, it might also need replacing.
Give this testing fuel injectors page a bookmark or share with a friend.
Tools for Testing Fuel Injectors
The The YouFixCars.com Homepage is a great place to find out what is covered on this automotive website. You can also discover how to get some do it yourself car repair help.
I have more information about diagnosing engines as well as the basics of operation. This next link takes you to this engine information section from this page about testing fuel injectors.